Today a bit about my first trials with Quick-fire Steel by Hadar Jacobson. I bought a jar of this clay more than a year ago, and simply forgot about it lying in my drawer. Finally I had decided to use it a few months ago, made a ton of notes, as usually when I'm working with a new material, but haven't put them together till now. Generally I have mixed feelings. I feel I need some more trials and this clay can give me more, but I'm a bit reluctant to use it again. AND it seems this clay is replaced with the new Low Shrinkage Quick-fire Steel XT. But get down to the nitty-gritty (wooohooo, I learned a new idiom ;) ).
Just like in case of Goldie Bronze, Quick-fire Steel by Hadar Jacobson comes in a form of powder you have to mix with water to get workable clay. Well - you probably all know famous Hadar's Clay™ :) - so I won't write about all the basics - just what I think were the most interesting observations and conclusions for me. This was the first clay by Hadar Jacobson I've ever used. I generally love the idea of steel jewellery so was hoping for the best.
This clay is definitely a ferromagnetic material. Well, no wonder as it contains mostly iron, but it was SO cool to see this :). The majority of my steel tools are slightly magnetized, and look what was happening (these are pliers dipped in steel clay powder). Lovely - fluffy pliers ^^'. So, optionally, this clay can be used in a demonstration of magnetic field lines ;).
It was very easy to make pliable clay out of the powder, but the clay
ready for use is a bit messy. I mean - no matter how much olive oil I put
on my hands, no matter how I modified amount of water - I was still getting SO dirty in contact with this
clay. The clay itself is quite nice to the touch - very rich, creamy,
beautiful brownish black, but for some reason it irritated my skin (I
have to say here, as a side note - I have very sensitive skin, so it's probably
just me.). It felt like there were some scrubbing particles in there.
Besides that the clay is very nice to work with. It can be textured very easily, it's very pliable - basically I could make all things I usually do without any problems. I decided to make a few rings, a simple pendant and two test pieces.
Firing was the worst part of the whole process. I used high fire schedule for muffle kiln:
1st phase: ramp at 1000°C to 593°C
2nd phase in coconut shell-based carbon: ramp at 1000°C to 971°C, 2 h hold.
Firstly - my stainless steel firing container was heavily distorted after this firing. Secondly - the inside surface of my kiln's door got three ugly cracks (the sound was quite scary!), and finally - the carbon was full of ash (definitely more ash than I get when I'm firing BRONZclay, Goldie Bronze or COPPRclay, even though I used a lid (Hadar Jacobson recommends NOT to use a lid, but I simply couldn't believe that this was a right thing to do ;). I just left a gap between firing pan and the lid). Later I consulted girls from Etsy Metal Clay Team and they confirmed that firing without a lid actually works.
So - generally firing time is quite long (you need to wait for a kiln to cool down after the 1st phase) and the firing temperature seems to be too high for my kiln and my firing container to bear (I have Prometheus PRO-7/PRG kiln). I definitely wouldn't mind if the firing temperature was a bit lower.
What's the most important of course - everything came out of the kiln sintered. But some other issues appeared. All pieces that had any flat surfaces were very grainy (I have to write here though that Hadar Jacobson says in her Quick-fire Steel Instruction Manual that the surface of non-textured steel is a little grainy, so this wasn't something unexpected). Major distortions also appeared.
I tried to straighten distorted pieces, but it was simply impossible - this steel is SO hard. But look at the test pieces. Here is little flat piece with a small ball. Ball was attached perfectly - I couldn't take it off with anything. I tried filing the piece and it revealed nice silver colour beneath grey, grainy surface.
I wanted to bend a coil a bit to check if it has any elasticity, but it was too hard! I couldn't bend it at all. The only thing I finally achieved with a few tools and a lot of force was breaking it. So this steel seems to be very, very strong, yet totally not elastic. Later I tried to forge it a bit and this gave it some elasticity.
These are two twig rings I made using Quick-fire Steel. I finished them using felt polishing wheel with a bit of polishing paste. I love this shiny finish and colour. It looks a bit like platinum, but it's so lightweight that it also reminds chromium. It's darker than silver, more grey and shinier. These rings weren't distorted in any way. Generally they survived firing just fine. Stones are cubic zirconias fired in place. If all pieces made of this clay fired so well I would be huge fan of it.
Here you can see better this beautiful mirror shine.
I also made a flat, rectangular ring and it turned out to be a total disaster. After firing it was heavily distorted. Rectangle shape wasn't rectangle anymore, the hole wasn't round - I had to make a lot of filing to make it look this way you see in the photo (and it still isn't perfectly rectangular). I also had to file down big grains that appeared on screws.
The last thing I made in this firing was a small, flat pendant with a lot of ornaments. I was totally not happy with it. The pendant wasn't flat anymore, everything was grainy, and the back of the pendant was very uneven. I tried to file it, but I gave up - it wasn't worth that much work.
It turned out I had a lot of clay left with water already added, so I covered it with olive oil, wrapped in plastic and planned to work with it the following day. Unfortunately in the morning I saw traces of rust in it, so decided to throw it away and make another portion. So it seems this clay, when mixed with water, has very short shelf life. No wonder - it isn't stainless steel after all. This rust thing inspired me to make one more trial, this time with rust added deliberately. I created a set of three rings and made second firing (this time firing temperature was 10 °C lower - I was hoping for less distortion and less grainy texture, but this didn't change anything - so again a lot of filing to make the holes round. At least this grainy texture works quite well here.).
Wonderful Jane Font gave me a recipe for making rust on steel. She told me to add some salt and vinegar to warm water, dip my pieces in it and let them dry. I wanted to speed up the process even more, so after dipping my pieces I put them into the kiln, which was still a bit warm after firing. It worked extremely fast. Here is the other side of the rings.
I know that rusting is an ongoing process, but it doesn't matter in case of these rings. To be honest they were not meant to be worn. They were made for a quite prestigious Polish contest, and now they are in an exhibition :).
So, generally, like I said, I have mixed feelings. I had some problems with this clay, but I love it's colour, possibilities of finishing and it's price ;). This grainy texture, which I don't like at all, will look very well on projects that are deliberately rough, very organic or tribal. I totally see possibilities of using it, but I prefer having more control over textures that appear on my projects. I would also love to have steel clay with slightly lower firing temperature. My poor kiln still works well, so nothing bad happened, but I was really stressed out ;). Maybe I'll use it again one day (I still have a half of a jar). I'm quite tempted to try this new Low Shrinkage Quick-fire Steel XT. Lower shrinkage should mean less distortion.
I also have another Hadar's Clay™ lying in my drawer and waiting to be used - white bronze. I hope I'll try it soon.
Wednesday, October 31, 2012
Monday, October 8, 2012
Flower storm
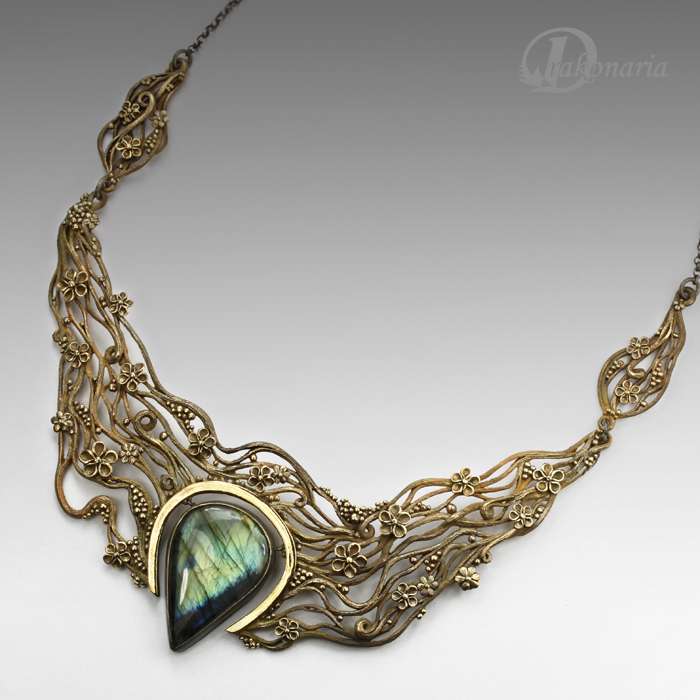
I'm so happy that one of my pieces got into Holly Gage's calendar :). It's the second time my work is published in this wonderful publication. This year it's my "Flower storm" necklace. I made it of Goldie Bronze, sterling silver and SO beautiful, blue-green labradorite. It was so much fun making it. Actually I think this was my biggest metal clay piece ever. It barely fitted my firing pan ;). Surprisingly I had totally no problems with firing it, so it was another successful trial with Waldo Iłowiecki's bronze.
It began as a sketch. I just drew a rough idea of the design around the stone. I have quite big collection of labradorite cabochons, and that day this one seemed to be particularly inspiring. I saw a storm inside it :) and wanted to use it in a dynamic, intricate design. I wanted to make something really big and openwork.
I formed the base of the necklace out of twig-like textured, thin coils. I like working on plexiglass, because I can put my sketches under it and they are still visible. This way I can easily use a sketch as a very accurate reference.
Then I added tiny balls and flowers...
...and decided that it would be nice to make two smaller elements, connecting the main part of the necklace with a chain I wanted to add later. I also added a plain "arch" to create nice contrast between rich organic ornaments and smooth, shiny surface.
Then I fired the piece ( I used the firing schedule I described in my post about Goldie Bronze™), made a soldered bezel cup for the stone and attached it to the main part. I added a few jump rings and a chain. The last thing to do was to slightly bend the necklace, to make it fit nicely a curvature of wearer's neckline. This bronze is really strong, so it wasn't a problem at all.
The same week I made also two other pieces similar in style. The first one was a "Flower storm" bangle, also with a labradorite cab. I wanted to check if it's possible to make strong and secure prong setting using Goldie Bronze. Totally positive. The second piece was a pair of earrings, adorned with flat, black pearls. It was quite tricky to make one earring look like a mirror image of another one, but I succeeded... more or less ;).
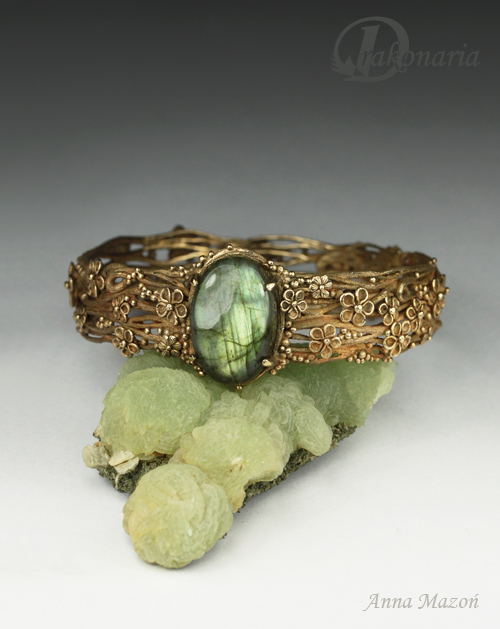

Well, enough about bronze for now. Recently I'm working with another wonderful material - green gold clay by Michelle Felice Glaeser! I also finally used my package of Art Clay 22K yellow gold clay ( I had it for 3 years ;D and it was still moist and pliable!). I'll write more about it soon :).
Subscribe to:
Posts (Atom)