Saturday, November 24, 2012
Green gold - REALLY? WOOW!!!
This was my first reaction when Michelle Glaeser asked me if I wanted to try her green gold clay. Green gold? Really? WOOOW!!! Of course I wanted to try it! With all my leaves, flowers and other organic ornaments, this was a dream come true, so I was waiting for a package with this precious material like for a birthday party ;).
Generally, I have to say I'm VERY impressed by this clay, how easy it is to use and how dramatic the final effect is. In my opinion it is extremely beautiful and unusual way to embellish a piece.
Below you can find photos of three projects I made with addition of this clay, and notes on what I learned while making them. So let the story begin :).
I got from Michelle about 0.7 g of her 18 K green gold clay, which is a bit less than a half of a regular batch she sells. 0.7 g... Right. I was just hoping I would see this batch without a magnifying glass ;).
When the package arrived I opened it holding my breath ;) and found this cute little jar, with clay wrapped in a kitchen plastic foil inside.
When I unwrapped the foil I immediately felt a smell of SO beautiful essential oils. Something like rose, sandalwood... Generally lovely, oriental fragrance. I'm looking at my notes, and I see I wrote down, that it smells like an India shop :). But it is seriously very pleasant and so unexpected. You get gold clay smelling like roses :). How cool is that?
The clay was very moist, but it had a bit uneven texture so I kneaded it for a while. I decided that the best way was to make it through the foil it came in. I didn't know the texture of this clay yet and definitely didn't want to end up with all I had stuck to my fingers. This way I got totally not sticky, perfectly moistured, smooth clay very quickly and without any stress.
Here you can see the size of the batch I got (less than a half of regular batch). It's light brown, not green at all. It may be surprising, but this gold turns green during sintering process. It's Michelle's secret how does this exactly work :).
As you can see the batch isn't big. At least I thought so, until I started working with it. I know it may sound unbelievable, but it's actually a lot of clay. I was sure I would use all the clay I had for the first ring I wanted to make. But it turned out, that I used about 1/3 of the batch and made twelve, quite big leaves. Overall I made, out of this one 0.7 g batch, 26 leaves and 12 balls which I used in three projects, and I still have a tiny bit of the gold left. It is simply because when you work with so precious material, you rather work small and smart.
The first thing I wanted to make was a silver twig ring, with a diamond, some flowers and green gold leaves. It was a whole "for the first time" experience. I used here PMC3 (and I've never used any kind of PMC before - we only have Art Clay distributor here in Poland), for the first time fired a diamond and, last but not least, for the first time I used this 18 K green gold.
I just put everything together with silver paste. Yes, you can fire this green gold with silver, simply greenware to greenware. Just put all elements together with silver paste, but make sure not to stain with silver paste any gold surfaces that will be visible. The clay dries quite slowely and has great workability.
Then I fired the ring. This gold can be fired in three different ways.
1. It can be torch fired, I haven't tried it though.
2. It can be fired in a kiln
3. It can be fired in a kiln in activated carbon
For this ring Michelle recommended the third option - firing in activated carbon - because of the diamond. It would be probably destroyed in any kind of open air firing. It is generally believed that fine silver clay needs to be fired in open air, but Michelle Glaeser found out that fine silver gets full shrinkage after 2 firings in carbon. She recommends 1505 ºF (818 ºC) for two hours, bring down to 200 ºF (circa 100 ºC), then fire again 1505 ºF for two hours. This 1505 ºF is a minimum temperature for the green gold, but you can go higher. What can I say - it works.
You can see in this photo how does green gold look like right after firing. It's already green - nice, light shade of green.
Here you can see, that, as expected, green gold doesn't react to LOS patina. It stays bright and clean against dark surface of oxidized silver.
And here you can see how the ready ring looks like. I made one photo with a piece of pyrite, to show a difference in colour between this yellow gold tone of the stone and greener shade of green gold. It can be easily polished with any tools you use for silver.
Then I decided to make something bigger, and more complicated. I made a rough sketch of an openwork pendant, a bit inspired by Art Nouveau, with faceted rubies, amethyst and green gold detailing (leaves, balls etc.).
Here you can see the pendant ready for firing. It had a lot more of green gold than the ring. I made some bigger leaves and balls. I had to work smart here and for example I flattened the balls to give them bigger, visible surface. Leaves are also made in a special way - they are green gold "doublets". I didn't want to make them too thick (it would be a waste of gold), so I paired them with silver leaves of exactly the same shape. I glued them together with silver paste, and added this strong, thick pieces to the pendant.
This time there was no need for carbon firing, so I fired the pendant simply in a kiln. I used generally the same firing schedule as previously, but went a little bit higher - 1540 ºF (838 ºC) for two hours, bring down to 200 ºF (circa 100 ºC), then fire again 1540 ºF for two hours.
The pendant came out of the kiln just perfect. You can see here again the shade of green gold right after firing.
I soldered a bezel for the amethyst and a jump ring, oxidized the piece, polished it partially and it was ready.
I'm pretty happy with the fact that this piece is both symmetrical and asymmetrical. I hope that this adds some movement and organic quality to the design. I named it "Once upon a time" ;). I'm still struggling with the chain... Maybe something else would be better. Originally I wanted to hang it on a strand of faceted amethysts, but it would be definitely too much.
Here is the last piece I made with green gold. Actually there is only a small addition of green gold in this ring (just leaves and a few tiny balls). It also contains yellow gold (22 K Art Clay Gold), silver (PMC3), two diamonds and lovely pale sapphire. You can see here the difference between 22K yellow gold and 18K green gold. In the next post, dedicated to yellow gold, I'll show you a few photos I took while making this piece. It was really great mixed metals fun :).
Like I said at the beginning, I really love this green gold clay by Michelle Glaeser. The final effect is simply fantastic and I appreciate the fact it can be fired in every possible way. It's also wonderful that it can be joined with silver greenware to greenware. Basically it has fine silver's simplicity of usage, but it brings to a piece truly precious quality.
Here you can find Michelle's blog: http://rosegoldclay.blogspot.com/
And here you can buy the clay: http://www.etsy.com/shop/mfglaeser
Friday, November 16, 2012
A season of gifts :)
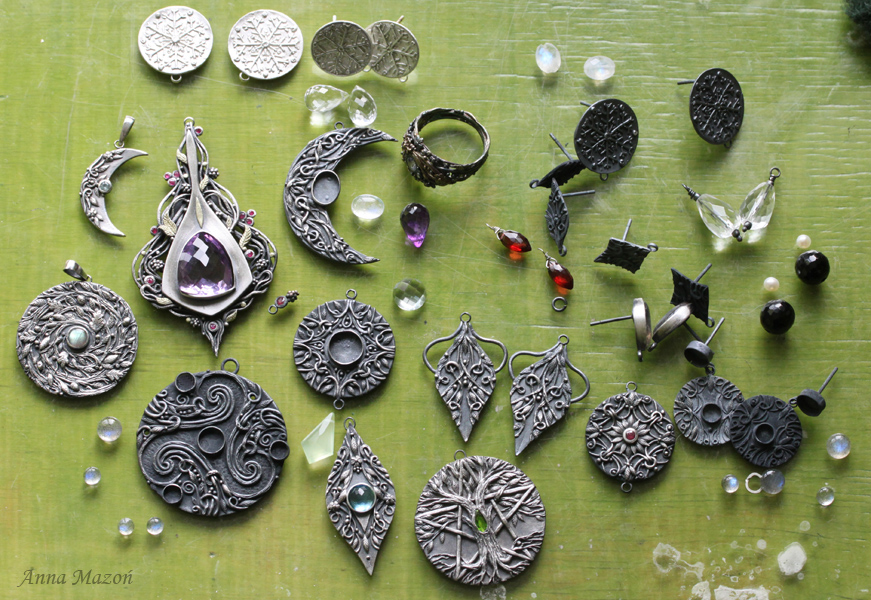
I'm very busy right now (well, who isn't? :) ) - a season of gifts is coming. I'm trying to make some things for sale and lots of custom orders. I have quite a hard time keeping control over all of this - I definitely have to formulate some neat email managing system - preferably Email Answering Fairy™...;)
Here you can see some of my work in progress. Some of these designs are new, some are older, but each time I recreate one of my designs I make it in a slightly different way. I believe we all deserve to wear really unique things :).
You can see it for example here. On the left there is my Spiral of Life design I made a year ago. It's a small, everyday pendant. In the middle there is version I made once in bronze. And on the right there is the newest version I finished yesterday. Each unique, each having its own character. This is the magic of handmade things and that's why they are the best gifts ever. :)
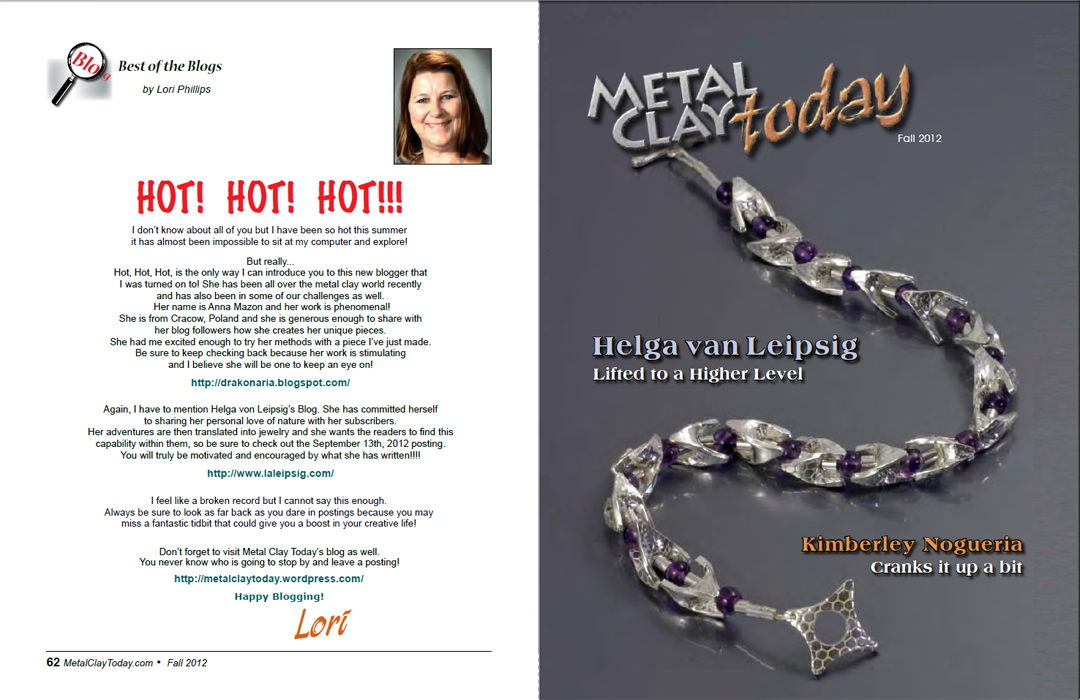
Ok, that's all for now I think, and I hope that next post will be (FINALLY) about Michelle Glaeser's green gold (SO GREAT!). You can see a few photos from my experiments on her blog already.
Wednesday, October 31, 2012
Quick-fire steel report
Today a bit about my first trials with Quick-fire Steel by Hadar Jacobson. I bought a jar of this clay more than a year ago, and simply forgot about it lying in my drawer. Finally I had decided to use it a few months ago, made a ton of notes, as usually when I'm working with a new material, but haven't put them together till now. Generally I have mixed feelings. I feel I need some more trials and this clay can give me more, but I'm a bit reluctant to use it again. AND it seems this clay is replaced with the new Low Shrinkage Quick-fire Steel XT. But get down to the nitty-gritty (wooohooo, I learned a new idiom ;) ).
Just like in case of Goldie Bronze, Quick-fire Steel by Hadar Jacobson comes in a form of powder you have to mix with water to get workable clay. Well - you probably all know famous Hadar's Clay™ :) - so I won't write about all the basics - just what I think were the most interesting observations and conclusions for me. This was the first clay by Hadar Jacobson I've ever used. I generally love the idea of steel jewellery so was hoping for the best.
This clay is definitely a ferromagnetic material. Well, no wonder as it contains mostly iron, but it was SO cool to see this :). The majority of my steel tools are slightly magnetized, and look what was happening (these are pliers dipped in steel clay powder). Lovely - fluffy pliers ^^'. So, optionally, this clay can be used in a demonstration of magnetic field lines ;).
It was very easy to make pliable clay out of the powder, but the clay ready for use is a bit messy. I mean - no matter how much olive oil I put on my hands, no matter how I modified amount of water - I was still getting SO dirty in contact with this clay. The clay itself is quite nice to the touch - very rich, creamy, beautiful brownish black, but for some reason it irritated my skin (I have to say here, as a side note - I have very sensitive skin, so it's probably just me.). It felt like there were some scrubbing particles in there.
Besides that the clay is very nice to work with. It can be textured very easily, it's very pliable - basically I could make all things I usually do without any problems. I decided to make a few rings, a simple pendant and two test pieces.
Firing was the worst part of the whole process. I used high fire schedule for muffle kiln:
1st phase: ramp at 1000°C to 593°C
2nd phase in coconut shell-based carbon: ramp at 1000°C to 971°C, 2 h hold.
Firstly - my stainless steel firing container was heavily distorted after this firing. Secondly - the inside surface of my kiln's door got three ugly cracks (the sound was quite scary!), and finally - the carbon was full of ash (definitely more ash than I get when I'm firing BRONZclay, Goldie Bronze or COPPRclay, even though I used a lid (Hadar Jacobson recommends NOT to use a lid, but I simply couldn't believe that this was a right thing to do ;). I just left a gap between firing pan and the lid). Later I consulted girls from Etsy Metal Clay Team and they confirmed that firing without a lid actually works.
So - generally firing time is quite long (you need to wait for a kiln to cool down after the 1st phase) and the firing temperature seems to be too high for my kiln and my firing container to bear (I have Prometheus PRO-7/PRG kiln). I definitely wouldn't mind if the firing temperature was a bit lower.
What's the most important of course - everything came out of the kiln sintered. But some other issues appeared. All pieces that had any flat surfaces were very grainy (I have to write here though that Hadar Jacobson says in her Quick-fire Steel Instruction Manual that the surface of non-textured steel is a little grainy, so this wasn't something unexpected). Major distortions also appeared.
I tried to straighten distorted pieces, but it was simply impossible - this steel is SO hard. But look at the test pieces. Here is little flat piece with a small ball. Ball was attached perfectly - I couldn't take it off with anything. I tried filing the piece and it revealed nice silver colour beneath grey, grainy surface.
I wanted to bend a coil a bit to check if it has any elasticity, but it was too hard! I couldn't bend it at all. The only thing I finally achieved with a few tools and a lot of force was breaking it. So this steel seems to be very, very strong, yet totally not elastic. Later I tried to forge it a bit and this gave it some elasticity.
These are two twig rings I made using Quick-fire Steel. I finished them using felt polishing wheel with a bit of polishing paste. I love this shiny finish and colour. It looks a bit like platinum, but it's so lightweight that it also reminds chromium. It's darker than silver, more grey and shinier. These rings weren't distorted in any way. Generally they survived firing just fine. Stones are cubic zirconias fired in place. If all pieces made of this clay fired so well I would be huge fan of it.
Here you can see better this beautiful mirror shine.
I also made a flat, rectangular ring and it turned out to be a total disaster. After firing it was heavily distorted. Rectangle shape wasn't rectangle anymore, the hole wasn't round - I had to make a lot of filing to make it look this way you see in the photo (and it still isn't perfectly rectangular). I also had to file down big grains that appeared on screws.
The last thing I made in this firing was a small, flat pendant with a lot of ornaments. I was totally not happy with it. The pendant wasn't flat anymore, everything was grainy, and the back of the pendant was very uneven. I tried to file it, but I gave up - it wasn't worth that much work.
It turned out I had a lot of clay left with water already added, so I covered it with olive oil, wrapped in plastic and planned to work with it the following day. Unfortunately in the morning I saw traces of rust in it, so decided to throw it away and make another portion. So it seems this clay, when mixed with water, has very short shelf life. No wonder - it isn't stainless steel after all. This rust thing inspired me to make one more trial, this time with rust added deliberately. I created a set of three rings and made second firing (this time firing temperature was 10 °C lower - I was hoping for less distortion and less grainy texture, but this didn't change anything - so again a lot of filing to make the holes round. At least this grainy texture works quite well here.).
Wonderful Jane Font gave me a recipe for making rust on steel. She told me to add some salt and vinegar to warm water, dip my pieces in it and let them dry. I wanted to speed up the process even more, so after dipping my pieces I put them into the kiln, which was still a bit warm after firing. It worked extremely fast. Here is the other side of the rings.
I know that rusting is an ongoing process, but it doesn't matter in case of these rings. To be honest they were not meant to be worn. They were made for a quite prestigious Polish contest, and now they are in an exhibition :).
So, generally, like I said, I have mixed feelings. I had some problems with this clay, but I love it's colour, possibilities of finishing and it's price ;). This grainy texture, which I don't like at all, will look very well on projects that are deliberately rough, very organic or tribal. I totally see possibilities of using it, but I prefer having more control over textures that appear on my projects. I would also love to have steel clay with slightly lower firing temperature. My poor kiln still works well, so nothing bad happened, but I was really stressed out ;). Maybe I'll use it again one day (I still have a half of a jar). I'm quite tempted to try this new Low Shrinkage Quick-fire Steel XT. Lower shrinkage should mean less distortion.
I also have another Hadar's Clay™ lying in my drawer and waiting to be used - white bronze. I hope I'll try it soon.
Just like in case of Goldie Bronze, Quick-fire Steel by Hadar Jacobson comes in a form of powder you have to mix with water to get workable clay. Well - you probably all know famous Hadar's Clay™ :) - so I won't write about all the basics - just what I think were the most interesting observations and conclusions for me. This was the first clay by Hadar Jacobson I've ever used. I generally love the idea of steel jewellery so was hoping for the best.
This clay is definitely a ferromagnetic material. Well, no wonder as it contains mostly iron, but it was SO cool to see this :). The majority of my steel tools are slightly magnetized, and look what was happening (these are pliers dipped in steel clay powder). Lovely - fluffy pliers ^^'. So, optionally, this clay can be used in a demonstration of magnetic field lines ;).
It was very easy to make pliable clay out of the powder, but the clay ready for use is a bit messy. I mean - no matter how much olive oil I put on my hands, no matter how I modified amount of water - I was still getting SO dirty in contact with this clay. The clay itself is quite nice to the touch - very rich, creamy, beautiful brownish black, but for some reason it irritated my skin (I have to say here, as a side note - I have very sensitive skin, so it's probably just me.). It felt like there were some scrubbing particles in there.
Besides that the clay is very nice to work with. It can be textured very easily, it's very pliable - basically I could make all things I usually do without any problems. I decided to make a few rings, a simple pendant and two test pieces.
Firing was the worst part of the whole process. I used high fire schedule for muffle kiln:
1st phase: ramp at 1000°C to 593°C
2nd phase in coconut shell-based carbon: ramp at 1000°C to 971°C, 2 h hold.
Firstly - my stainless steel firing container was heavily distorted after this firing. Secondly - the inside surface of my kiln's door got three ugly cracks (the sound was quite scary!), and finally - the carbon was full of ash (definitely more ash than I get when I'm firing BRONZclay, Goldie Bronze or COPPRclay, even though I used a lid (Hadar Jacobson recommends NOT to use a lid, but I simply couldn't believe that this was a right thing to do ;). I just left a gap between firing pan and the lid). Later I consulted girls from Etsy Metal Clay Team and they confirmed that firing without a lid actually works.
So - generally firing time is quite long (you need to wait for a kiln to cool down after the 1st phase) and the firing temperature seems to be too high for my kiln and my firing container to bear (I have Prometheus PRO-7/PRG kiln). I definitely wouldn't mind if the firing temperature was a bit lower.
What's the most important of course - everything came out of the kiln sintered. But some other issues appeared. All pieces that had any flat surfaces were very grainy (I have to write here though that Hadar Jacobson says in her Quick-fire Steel Instruction Manual that the surface of non-textured steel is a little grainy, so this wasn't something unexpected). Major distortions also appeared.
I tried to straighten distorted pieces, but it was simply impossible - this steel is SO hard. But look at the test pieces. Here is little flat piece with a small ball. Ball was attached perfectly - I couldn't take it off with anything. I tried filing the piece and it revealed nice silver colour beneath grey, grainy surface.
I wanted to bend a coil a bit to check if it has any elasticity, but it was too hard! I couldn't bend it at all. The only thing I finally achieved with a few tools and a lot of force was breaking it. So this steel seems to be very, very strong, yet totally not elastic. Later I tried to forge it a bit and this gave it some elasticity.
These are two twig rings I made using Quick-fire Steel. I finished them using felt polishing wheel with a bit of polishing paste. I love this shiny finish and colour. It looks a bit like platinum, but it's so lightweight that it also reminds chromium. It's darker than silver, more grey and shinier. These rings weren't distorted in any way. Generally they survived firing just fine. Stones are cubic zirconias fired in place. If all pieces made of this clay fired so well I would be huge fan of it.
Here you can see better this beautiful mirror shine.
I also made a flat, rectangular ring and it turned out to be a total disaster. After firing it was heavily distorted. Rectangle shape wasn't rectangle anymore, the hole wasn't round - I had to make a lot of filing to make it look this way you see in the photo (and it still isn't perfectly rectangular). I also had to file down big grains that appeared on screws.
The last thing I made in this firing was a small, flat pendant with a lot of ornaments. I was totally not happy with it. The pendant wasn't flat anymore, everything was grainy, and the back of the pendant was very uneven. I tried to file it, but I gave up - it wasn't worth that much work.
It turned out I had a lot of clay left with water already added, so I covered it with olive oil, wrapped in plastic and planned to work with it the following day. Unfortunately in the morning I saw traces of rust in it, so decided to throw it away and make another portion. So it seems this clay, when mixed with water, has very short shelf life. No wonder - it isn't stainless steel after all. This rust thing inspired me to make one more trial, this time with rust added deliberately. I created a set of three rings and made second firing (this time firing temperature was 10 °C lower - I was hoping for less distortion and less grainy texture, but this didn't change anything - so again a lot of filing to make the holes round. At least this grainy texture works quite well here.).
Wonderful Jane Font gave me a recipe for making rust on steel. She told me to add some salt and vinegar to warm water, dip my pieces in it and let them dry. I wanted to speed up the process even more, so after dipping my pieces I put them into the kiln, which was still a bit warm after firing. It worked extremely fast. Here is the other side of the rings.
I know that rusting is an ongoing process, but it doesn't matter in case of these rings. To be honest they were not meant to be worn. They were made for a quite prestigious Polish contest, and now they are in an exhibition :).
So, generally, like I said, I have mixed feelings. I had some problems with this clay, but I love it's colour, possibilities of finishing and it's price ;). This grainy texture, which I don't like at all, will look very well on projects that are deliberately rough, very organic or tribal. I totally see possibilities of using it, but I prefer having more control over textures that appear on my projects. I would also love to have steel clay with slightly lower firing temperature. My poor kiln still works well, so nothing bad happened, but I was really stressed out ;). Maybe I'll use it again one day (I still have a half of a jar). I'm quite tempted to try this new Low Shrinkage Quick-fire Steel XT. Lower shrinkage should mean less distortion.
I also have another Hadar's Clay™ lying in my drawer and waiting to be used - white bronze. I hope I'll try it soon.
Monday, October 8, 2012
Flower storm
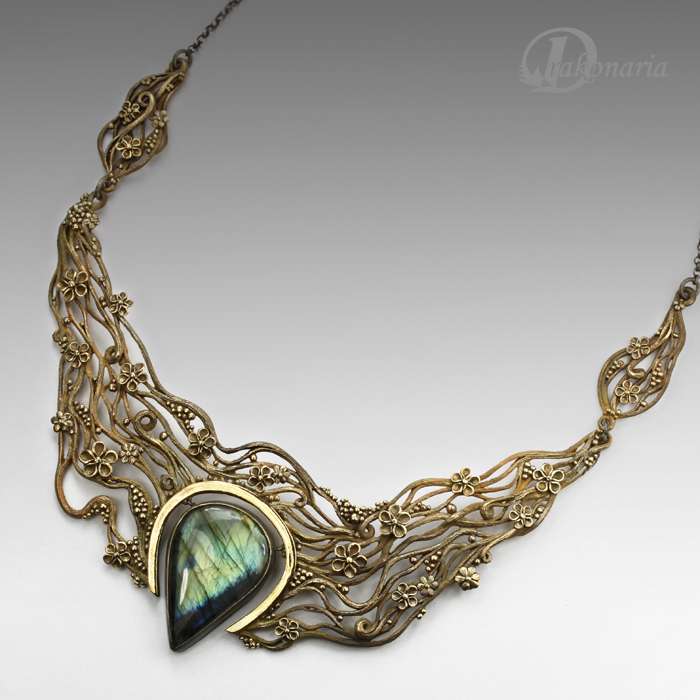
I'm so happy that one of my pieces got into Holly Gage's calendar :). It's the second time my work is published in this wonderful publication. This year it's my "Flower storm" necklace. I made it of Goldie Bronze, sterling silver and SO beautiful, blue-green labradorite. It was so much fun making it. Actually I think this was my biggest metal clay piece ever. It barely fitted my firing pan ;). Surprisingly I had totally no problems with firing it, so it was another successful trial with Waldo Iłowiecki's bronze.
It began as a sketch. I just drew a rough idea of the design around the stone. I have quite big collection of labradorite cabochons, and that day this one seemed to be particularly inspiring. I saw a storm inside it :) and wanted to use it in a dynamic, intricate design. I wanted to make something really big and openwork.
I formed the base of the necklace out of twig-like textured, thin coils. I like working on plexiglass, because I can put my sketches under it and they are still visible. This way I can easily use a sketch as a very accurate reference.
Then I added tiny balls and flowers...
...and decided that it would be nice to make two smaller elements, connecting the main part of the necklace with a chain I wanted to add later. I also added a plain "arch" to create nice contrast between rich organic ornaments and smooth, shiny surface.
Then I fired the piece ( I used the firing schedule I described in my post about Goldie Bronze™), made a soldered bezel cup for the stone and attached it to the main part. I added a few jump rings and a chain. The last thing to do was to slightly bend the necklace, to make it fit nicely a curvature of wearer's neckline. This bronze is really strong, so it wasn't a problem at all.
The same week I made also two other pieces similar in style. The first one was a "Flower storm" bangle, also with a labradorite cab. I wanted to check if it's possible to make strong and secure prong setting using Goldie Bronze. Totally positive. The second piece was a pair of earrings, adorned with flat, black pearls. It was quite tricky to make one earring look like a mirror image of another one, but I succeeded... more or less ;).
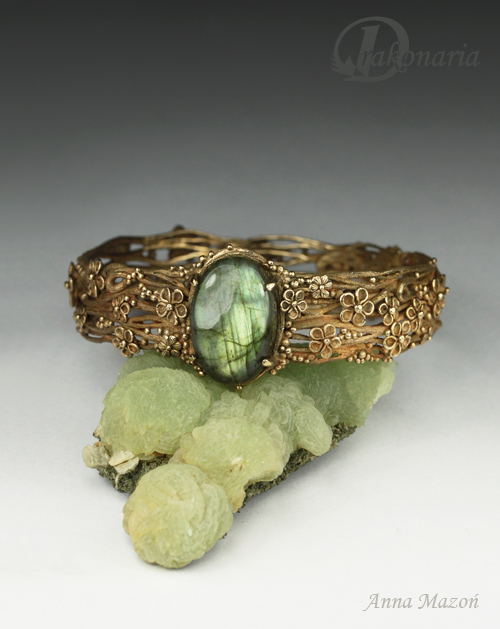

Well, enough about bronze for now. Recently I'm working with another wonderful material - green gold clay by Michelle Felice Glaeser! I also finally used my package of Art Clay 22K yellow gold clay ( I had it for 3 years ;D and it was still moist and pliable!). I'll write more about it soon :).
Saturday, September 22, 2012
"Herbarium" openwork pendant workshop
I have really wonderful news to share :). Next year I'll teach a class on my openwork "Herbarium" pendants in Lynne Glazzard's workshop in beautiful Yorkshire, UK. The class will take place on 11th and 12th May 2013. You can find all the information here, on Metal Clay North website.
So, if you like my work, would like to learn something from me, but Poland is too far, maybe UK is an option to check out :).
This is an offcial description of the workshop:
"In this class you will learn to make an openwork, romantic pendant, adorned with a bezel set stone and precise, tiny ornaments. You will use silver clay to create lacy, yet strong and secure constructions, which you’ll decorate with extremely detailed tiny leaves, flowers, forest fruits or other ornaments of your choice. You will also learn to make a box like, elevated base for a stone and set it in a bezel setting. All these skills can be easily adapted to your own style, merged with your favourite techniques and used with different metal clays. Openwork designs are wonderful response to increasing silver prices, allowing you to save on material, but not on the quality of your works. Some previous silver clay experience is necessary."
And here are a few bigger projects I made using this technique:
I hope it's tempting ;). I'm very excited about teaching in Lynne Glazzard's studio. And, if UK is still too far, you can always check my tutorials in my Etsy shop :).
P.S. I'll also teach this class in Poland soon. More news coming.
So, if you like my work, would like to learn something from me, but Poland is too far, maybe UK is an option to check out :).
This is an offcial description of the workshop:
"In this class you will learn to make an openwork, romantic pendant, adorned with a bezel set stone and precise, tiny ornaments. You will use silver clay to create lacy, yet strong and secure constructions, which you’ll decorate with extremely detailed tiny leaves, flowers, forest fruits or other ornaments of your choice. You will also learn to make a box like, elevated base for a stone and set it in a bezel setting. All these skills can be easily adapted to your own style, merged with your favourite techniques and used with different metal clays. Openwork designs are wonderful response to increasing silver prices, allowing you to save on material, but not on the quality of your works. Some previous silver clay experience is necessary."
And here are a few bigger projects I made using this technique:
![]() |
"Herbarium - Misty Morning" - silver, green quartz, topaze |
![]() |
"Herbarium - spring rainbow" - ACS silver and labradorite |
![]() |
"Herbarium - blackberry" - ACS silver and amethyst |
![]() |
"Herbarium - summer scent" - silver, 22 K gold, labradorites |
![]() |
"Herbarium - forest flame" - fine silver and labradorite |
![]() |
"Herbarium - forest fruits" - silver, amethyst and garnet |
![]() |
"Herbarium - raspberry" - bronze ring with garnet |
![]() |
"Herbarium - gold vines" - bronze and olivine |
P.S. I'll also teach this class in Poland soon. More news coming.
Subscribe to:
Posts (Atom)